Bringing On-Farm Fluid Fertilizer Storage into Compliance: What Will It Cost?*
June 16, 1992
PAER-1992-7
Duane Rogers, Graduate Research Assistant; and Jay T. Akridge, Associate Professor, and Associate Director of Center for Agricultural Business
There has been increasing concern regarding the effect of agriculture pesticides and fertilizers on our water supply. Much attention has focused on residues which have been detected in a small number of rural water wells (EPA). In response to this increased public concern, federal and state governments have passed legislation affecting the handling and use of many fertilizers and pesticides.
The Indiana State Chemist recently adopted guidelines for the construction of fertilizer and pesticide storage containment facilities (Indiana State Chemist and Seed Commissioner, 1991 lb; 1991c). These facilities are to contain any spills which might occur during the storage or handling of fertilizers and pesticides. The rules will affect many Indiana agribusiness firms, as well as farmers who store these products on their farms. Thus, many Indiana farmers will need to decide whether to upgrade their storage facilities to comply with the new regulations or to abandon their on-farm storage program.
This article discusses the costs involved in bringing on-farm storage facilities for fluid fertilizers into compliance. Compliance costs for two typical on-farm storage tank sizes are presented. In addition, the steps for evaluating the decision of whether to upgrade or abandon storage facilities are outlined.
The Rules
The Indiana State Chemist adopted two sets of rules on containment of fertilizers and pesticides. The rules governing bulk pesticide storage went into effect May 7, 1991 (Indiana State Chemist and Seed Commissioner, 1991 b). The rules which govern bulk fertilizer storage went into effect July 6, 1991 (Indiana State Chemist and Seed Commissioner, 1991c).** These rules apply to anyone who stores bulk pesticides and fertilizers in excess of specified minimum amounts. The law makes no distinction between farmers and agribusiness firms -Indiana fa1mers must comply with the rules if they store pesticides and fertilizers in quantities which exceed the specified minimums.
What are the minimums? For fertilizer products, any location which stores more than 2,500 gallons of fluid fertilizer in undivided quantities or more than 12 tons of dry bulk fertilizer in undivided quantities must comply with the rules (Indiana State Chemist and Seed Commissioner, 1991 c). The term “undivided quantities” simply means ‘stored in a single container.’ This says that while a fa1mer with one 3,000-gallon fertilizer storage tank would need to comply with the new rules, a farmer with six 500-gallon tanks would not.
For dry pesticide products, any location where more than 100 pounds of dry pesticides are stored in undivided quantities will need to comply. For fluid pesticides, the minimum is 55 gallons (Indiana State Chemist and Seed Commissioner, 199 lb). The one exception to this rule is if the products are stored in ‘mobile containers’ for less than 15 days. A ‘mobile container’ is basically any container that is on wheels and can be readily moved. Minibulk containers normally filled by dealers, loaded onto vehicles, and transported to the farm or field are considered mobile (Indiana State Chemist and Seed Commissioner, 1991c).
While Indiana farmers must be familiar with all rules, the rules pertaining to fluid fertilizer storage will likely have the biggest impact on Hoosier farmers. Given the widespread practice of storing fluid fertilizers on the farm, the remainder of this article focuses on the fluid fertilizer rules.
To bring fluid storage facilities into compliance, two types of containment facilities must be erected. The rules state that there must be a facility (dike) capable of containing any spill due to failure of the storage tank. In addition, an operational area containment pad is required to contain any spill that occurs during the loading or unloading of the storage tank.
The regulations state that the diked area around the storage tank(s) must be large enough to contain the volume of the largest tank plus the volume displaced by all tanks and equipment inside the containment area. An extra six inches (free board space) must be added to the height of the wall to accommodate rainfall.
The operational area containment pad must be constructed and reinforced to handle the maximum gross load (including product) of any vehicle using the operational area. The operational area must at least IO feel wide and 20 feet long. The curbed surface and catch basin of the area must be large enough to hold at least 750 gallons of discharged fluid (Indiana State Chemist and Seed Commissioner, 1991 c).
The Example
For this analysis, two storage tank sizes commonly used on Indiana farms were chosen – 6,000 and 10,000 gal Ions. The cost estimates presented in this article were developed with the assistance of a construction company. The actual cost of bringing your own storage facility into compliance may be quite different from the figures presented here. However, the method used to calculate the costs is general and should provide an example to follow when calculating your costs. There are five steps which are important to follow when making the upgrade or abandon decision. These steps are outlined below.
Step I – Choose Diking Material
The first step in the analysis is to decide on the appropriate material to be used for construction of the containment facility. Concrete is used in the example presented here, but other materials such as synthetic or clay/earthen liners could also be used (Indiana State Chemist and Seed Commissioner, 1991 c; Solutions). Note that this is a fundamental decision, and it is important to check with the State Chemist if there are any questions as to the nature of the materials used or the construction plan itself.
Step II – Calculate Initial Investment Costs
The second step consists of estimating the cost of building the containment structures. Since some farmers may use their own labor. the cost of construction has been broken into two categories, labor and materials. For the two example tanks, the cost estimates are shown in Table 1. (Appendix A presents detail on the specifications of the structures.) For the 6,000-gal Ion storage tank, the cost of the 17’x 17′ x 3′-6″ dike required to comply with the regulations would be $6,324. For the load/unloading pad, the minimum allowable size was used. Thus, the load/unloading pad measures JO’ x 20′ and cost $1,473 to build. The total initial investment required to bring this 6,000-gallon tank into compliance is $7,797. For the 10,000-gallon tank, a 22′ x 22′ x 3′-6″ dike is required. The total investment for the dike and load/unloading pad with the larger tank is $9,712. Cost estimates obtained from other construction firms for the 6,000-gallon tank ranged from$6,000 and $6,500 for the combined dike and load/unloading pad. For the I 0,000-gallon tank, cost estimates ranging from $7,900 to $9,015 were obtained. Obviously, there can be wide differences in costs and it is recommended that you consult with more than one construction company when seeking estimates. Note also that there are considerable scale economies involved – a 66% increase in tank capacity requires only a 25% increase in the initial investment. Note also that the total initial investment cost is split roughly 50/50 in terms of labor and materials.
There are two costs which were not included in the cost estimates. First, the cost of physically moving the tank onto the load/unloading pad was excluded. In addition, the cost of a pump to transfer any spill liquid f om the containment area into a holding tank was not included. These costs would vary with each individual situation.
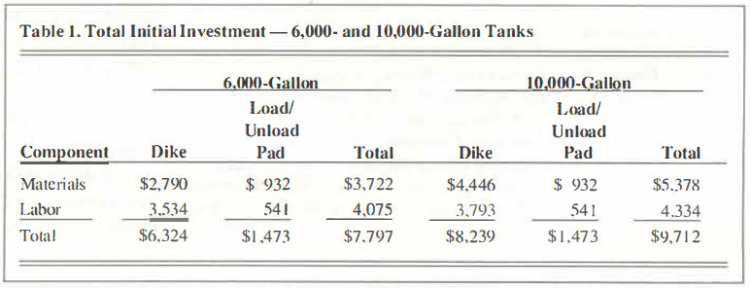
Table 1. Total Initial Investment – 6,000 and 10,000 Gallon Tanks
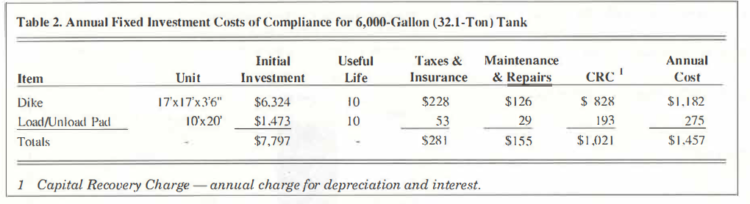
Table 2. Annual Fixed Investment Costs of Compliance for 6,000 Gallon (32.1 ton) tank
Step Ill – Calculate Annual Ownership Costs
The third step in the analysis is to convert the initial investment cost into an annual ownership cost. For our analysis, a long-term interest rate of I 0.5% and an annual inflation rate of 5% is used. The containment structure is assumed to have a I 0-year useful life with no salvage value at the end of its useful life. The calculations used to determine annual ownership costs are shown in Table 2 and Table 3.
The column labeled ‘Taxes & Insurance’ in each table refers to the increase in property taxes and insurance resulting from construction of the containment facilities. For the example, annual taxes and insurance are assumed to increase annually by 3.6% of the initial investment cost (Simpson). The column titled ‘Maintenance & Repairs’ refers to the cost of repairing and maintaining the containment facilities. Annual maintenance and repairs are assumed to be 2% of the initial investment (Simpson).
The last column of Table 2 is titled ‘CRC,’ an abbreviation for ‘Capital Recovery Charge.’ The CRC is simply the annual cost associated with depreciation and interest. This formula annualizes the cost of depreciation and interest using the real rate of interest (rate of interest with inflation removed) over the life of the asset. (Additional information on the CRC calculation is presented in Appendix B.)
Summing the three columns in Table 2 shows the annual cost for the 6,000-gallon tank dike is $1,182. In addition, the annual ownership cost for the load/unloading pad is $275. The total annual cost of compliance for the 6,000-gallon tank is $1,457. Using the same method of calculation for the I 0,000-gallon tank, the annual cost is $1,816 (Table 3).
Step IV – Calculating Annual Per-Ton Costs
One way to look at the cost issue is to express cost on a per-ton basis; that is, what is the annual compliance cost per ton of product stored? This per-ton cost can then be compared to the benefits which might accrue to on-farm storage, such as lower product prices.
The first step in calculating an annual per-ton cost is to convert the tank capacity from gallons to tons. The 6,000-gallon tank has a capacity of approximately 32.1 tons of fluid fertilizer. To obtain this figure, the tank’s capacity (6,000 gallons) is multiplied by the weight per gallon of 28% nitrogen solution (10.7 lbs/gallon), and the resulting amount is divided by 2,000 (lbs/ton). Following the same procedures for the 10,000-gallon tank, the capacity in tons is approximately 53.5.
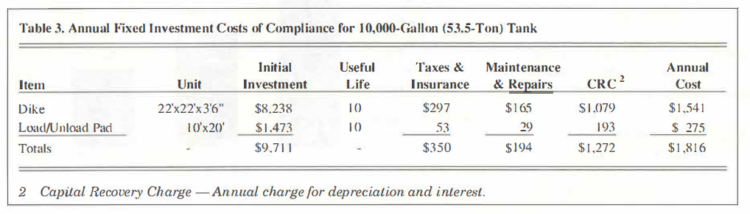
Table 3. Annual Fixed Investment Costs of Compliance for 10,000 Gallon (53.5 ton) Tank
The next step is to divide the annual ownership cost by the number of tons of material moving through the tank during the year. In this example, three levels of throughput were considered:
► filling and unloading each tank once a year
► twice a year
► three times a year
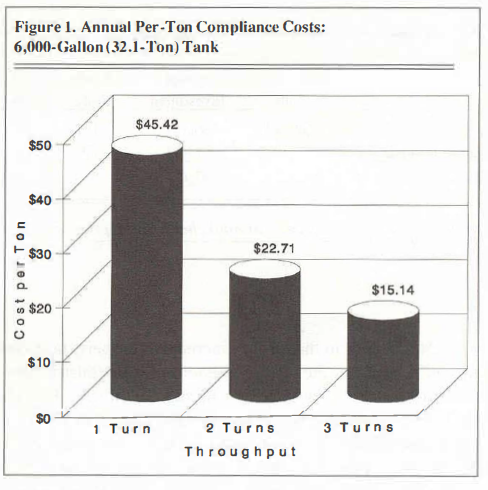
Figure 1. Annual Per-Ton Compliance Costs: 6,000 Gallon (32.1 Ton) Tank
For the 6,000-gallon tank, the annual throughput associated with filling and unloading the tank once a year is 32.1 tons. The annual throughput for two and three times per year is 64.2 and 96.3 tons, respectively. Obviously. the higher the throughput figure, the lower the annual per-ton cost.
The impact of throughout on annual cost for the 6,000-gallon tank is shown in Figure I. For one turn, the annual cost is $45.42 per ton. It is $22.71 per ton for two turns, and $ l 5 .14 per ton for three turns. Repeating the same procedure for the I 0.000-gallon (53.5-ton) tank gives per-ton costs of $33.94, $16.97, and $11.31, for one, two. and three fillings per year, respectively (Figure 2).
The costs associated with upgrading facilities to comply with the new rules concerning secondary and operational area containment are significant. There are substantial economies of scale involved-costs drop dramatically as throughput is increased. To make upgrading your facilities economically feasible. you would need to be able to obtain fluid fertilizer at a much lower price or obtain other substantial benefits from on-farm storage.
Step V -Compare Costs and Benefits
To complete the analysis, the annual per-ton ownership cost should be compared to the benefits of on-farm storage. The most likely benefits are:
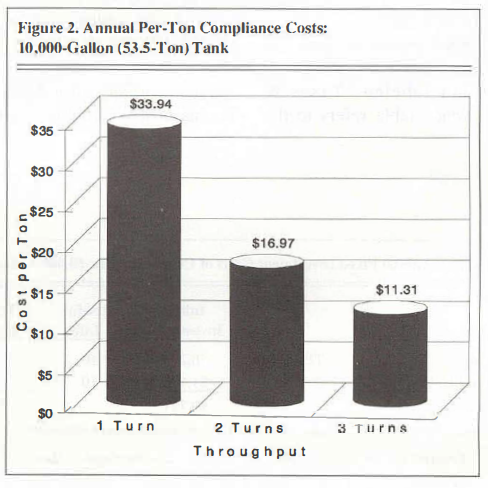
Figure 2. Annual Per-Ton Compliance Costs: 10,000 Gallon (53.5 Ton) Tank
► savings in the form of a lower price as a result of being able to store material on your farm
► convenience of having fluid fertilizer available when you need it, instead of relying on your local fertilizer supplier to deliver fertilizer to you in the busy spring season.
► the purchasing flexibility associated with having your own storage facilities
By having your own storage facility, you can buy and pay for fertilizer whenever it is most advantageous to do so. By buying fertilizer in the off-season, you may be able to realize a substantial cost savings. Benefits such as a lower product price, convenience, and purchasing flexibility must be compared against the per-ton cost to arrive at the decision that is best for you.
Summary
In summary, the procedure for deciding on the appropriate plan of action is fivefold. First, identify the construction material which is best suited for your particular situation. We have only evaluated one such alternative, concrete. Some synthetic and clay/earthen materials may also be used for diking purposes and these options may be more cost effective than concrete. After selecting the diking material, the second step is to calculate the initial investment cost associated with that material. The third step involves converting the initial investment cost, along with all other relevant costs, into an annual ownership cost. In the fourth step, the annual ownership cost is converted to an annual per-ton cost. The final step is to compare the costs to the benefits of on-farm storage. Following these steps should put you in a better position to make the correct upgrade or abandon decision on your farm.
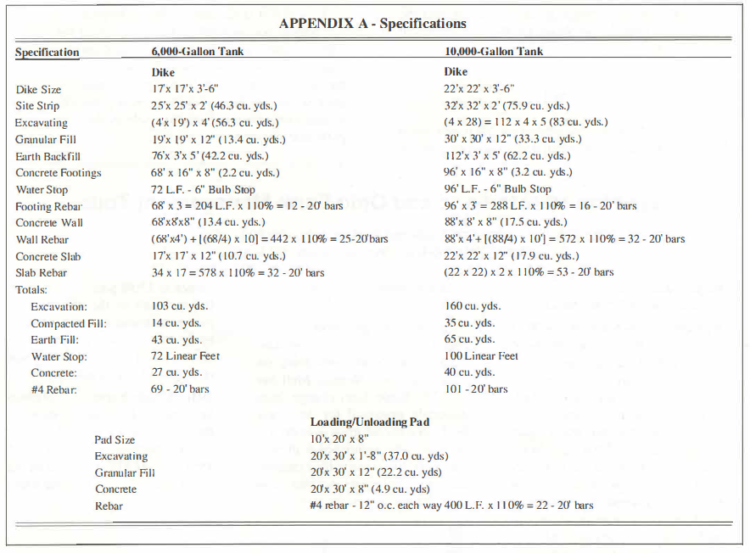
Appendix A. Specifications
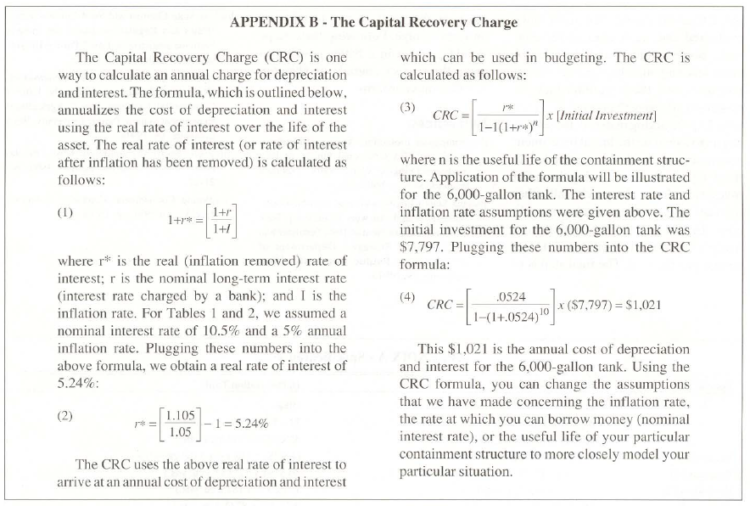
Appendix B. The Capital Recovery Change
References
Environmental Protection Agency. ‘·Summary Results or EPA’s National Survey of Pesticides in Drinking Water Wells.”‘ National Pesticide Survey. Fall 1990.
Indiana State Chemist and Seed Commissioner. “Questions and Answers Concerning New Rules for Containment of Bulk Fertilizer and Ag Chemical Storage.” Department of Biochemistry. Purdue University, West Lafayette, IN, 1991a.
Indiana State Chemist and Seed Commissioner. “Rules and Regulations Under the Indiana Pesticide Registration Law.” Purdue University, West Lafayette. IN, 1991b.
Indiana State Chemist and Seed Commissioner. “Rules and Regulations Under the Indiana Commercial Fertilizer Law.” Agricultural Experiment Station. Purdue University. West Lafayette, IN. 1991c.
Simpson, Scott. “Containment Cost Calculations.” Dealer Progress. January I 991. pp.
21-22.
“Exploring Containment Materials.” Solutions. July/August 1991. pp. 16-18.
* Funding for this project was provided by the Tennessee Valley Authority National Fertilizer and Environmental Research Center and Purdue University. The authors gratefully acknowledge the helpful comments of Timothy Baker, Lee Schrader, Chris Hurt, and Bob Rund on an earlier draft of this paper. Special thanks to Tim Gorman for his help in developing the cost estimates.
** These rules are outlined in two publications entitled “Rules and Regulations Under the Indiana Pesticide Registration Law” and “Rules and Regulations Under the Indiana Commercial Fertilizer Law.” Copies of these publications can be obtained by contacting the Indiana State Chemist Office, Purdue University, West Lafayette, IN 47907.