Is This Pesticide On My Shelf Still Good?
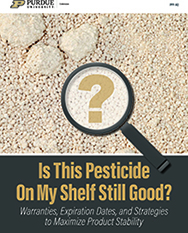
Fred Whitford, Director, Purdue Pesticide Programs
Joe Becovitz, Pesticide Program Specialist, Office of Indiana State Chemist
Douglas Linscott, Formulation Chemist, Corteva Agriscience, LLC
John Obermeyer, IPM Specialist, Purdue University
Bob Hill, Consultant, Robert Hill Consultants, LLC.
Kevin Leigh Smith, Continuing Lecturer and Communication Specialist,
Purdue Agricultural Sciences Education and Communication
Expiration Date and Shelf Life …………………………………………………….. 4
Quantifying a Formulation’s Stability……………………………………………. 7
Stability Linked to Formulation Components……………………………….. 9
Storage Restrictions on Labels …………………………………………………15
Answering the Question: ‘Is the Product Still Good?’ ……………………..16
Storing Products Within the First Three Years …………………………….. 17
Evaluating Products of Questionable Age …………………………………. 20
Conclusion …………………………………………………………………………….. 26
Find Out More…………………………………………………………………………. 28
Acknowledgments…………………………………………………………………… 30
Disclaimer ……………………………………………………………………………… 30
Expiration Date and Shelf Life
You may have seen supermarket shoppers reaching to the back of the cooler for what they perceive to be the “freshest” milk. You are used to checking perishable foods (milk, eggs, meat, bread, juices, and more) for the expiration dates or “Best if used by” dates stamped on them to make sure you are not buying items that will soon spoil.
Canned food items have expiration dates, too. But unlike perishable products, their expiration dates are years after the products were processed and preserved. The products inside cans often include preservatives that were added to maintain freshness, and those canned products were pasteurized and sealed against air, moisture, and microbial contamination.
Which raises the question: “Why can I open these canned products after the expiration date and they still look and taste good?” The difference between a product’s expiration date and its actual shelf life may be different.
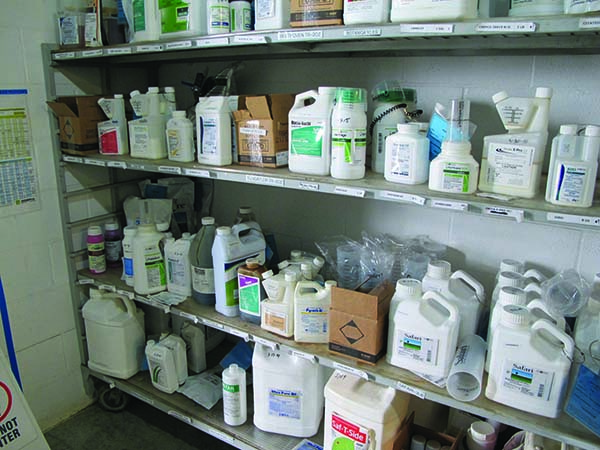
With fresh, perishable products, the expiration dates and shelf life are usually the same; however, the shelf life of nonperishable products often extends well beyond their expiration dates.
Consider that durable goods often provide warranty periods, which begin on the date of purchase and extend for a period of time. With durable goods, the warranty is analogous to the expiration date. But whether it’s a watch, a water heater, or a vehicle, we all expect our durable goods to function well beyond their warranty periods.
In other words, a durable good’s longevity (or shelf life) will most likely exceed its warranty (or expiration date).
One of the challenges we face as consumers is extending the life of products we purchase. For example, the life of a truck depends on many factors, including servicing it at regular intervals, keeping the exterior clean, practicing safe driving habits, and reducing the number of miles you drive each year.
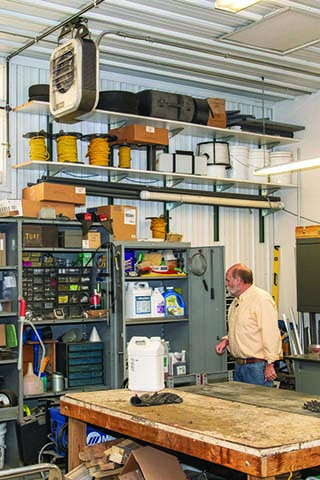
Expiration date, warranty, and shelf life are all terms that apply to pesticides too. Farmers and commercial applicators want to know how long they can store pesticide products without losing their efficacy. How long a pesticide will remain effective becomes more difficult to determine if, in addition to being past its expiration or warranty date, the product was opened or stored without protection from moisture, extreme heat, and cold.
If you leave a gallon of milk open on the counter overnight, you know it will sour even though it still has a week left on its expiration date. If you open a can of green beans and store it in the refrigerator, the beans will most certainly go bad well before the expiration date listed on the can. Likewise, how long a pesticide can last in storage depends on many factors including its formulation, active ingredient(s), age, storage conditions, and whether it remained sealed or was opened.
If you use a pesticide product beyond its expiration date, it may or may not be less effective. Using a pesticide product beyond its expiration date doesn’t necessarily mean the product has degraded to the point that it is no longer effective. Then again, there’s no guarantee that it hasn’t degraded. There are too many factors that can degrade the product (like storage conditions) that are beyond the manufacturer’s control. That is why manufacturers make no assurances or warranties about the quality of their products after the expiration date.
This publication provides an overview of the processes that are used to determine a pesticide product’s storage stability and explores options for what you can do when these products expire. Our overall goal is to encourage you follow best practices when storing pesticides, so you never have to wonder, “Is the product on my shelf still good?”
Clarifying the Terms
Expiration date, shelf life, and warranty are often used interchangeably, but they have different meanings.
Manufacturers set expiration dates. The expiration date tells you that a properly stored product will perform as expected if you use it before the expiration date.
Warranties are normally provided for durable goods and are analogous to the expiration dates for perishable products. A pesticide’s warranty assures you that there is a period of time that it is guaranteed to work and will be replaced if it does not.
Shelf life is how long the product will remain effective after its expiration date and warranty have passed. Storage conditions greatly influence how fast a product degrades. That is why there is no set time for the long-term stability of pesticide formulations.
Quantifying a Formulation’s Stability
The U.S. Environmental Protection Agency (EPA), under the Federal Insecticide, Fungicide, and Rodenticide Act (FIFRA) requires all pesticide products to meet active ingredient stability and product quality specifications. No new pesticide product may be sold until the EPA assures the product meets all these requirements.
Stable Concentration
First, the concentration of the active ingredient must remain stable when stored under conditions that simulate two years of real-time aging. While this is a general requirement, products will remain within their specification range much longer. This assures the active ingredient’s potency meets its label claim while in storage and will reliably provide consistent field performance.
Stable Physical Structure
Second, the EPA requires the product to remain physically stable for two years (for example, it does not irreversibly clump or separate). To meet these requirements, manufacturers must develop and submit test data performed under good laboratory practices to demonstrate the product remains physically stable before it is released for sale. Manufacturers test products for an array of conditions (such as extreme temperatures) that products might encounter in storage.
Stable Packaging
Third, the product formulation requires in-package testing to confirm that there is no risk of spills or leaks. Furthermore, manufacturers must ensure the packaging material itself does not create problems with product formulation.
Testing the physical stability of a product focuses on how effectively its inert ingredients support the delivery of its active ingredient. In other words, does the product still mix, suspend, and disperse? Inert materials that degrade, or are used in insufficient amounts, may lead to premature product separation or even failures. Manufacturers need to optimize the inert ingredient levels to provide a product that is high enough in viscosity to remain stable and remixable, but not so viscous that it becomes difficult to pump or pour.
Coformulants that degrade can lead to inconsistent product application. For instance, when subjected to freezing temperatures, the active ingredient could crystalize and fall out of suspension, settle to the bottom, and not resuspend when thawed and remixed.
When manufacturers evaluate a formula’s physical properties, they also analyze the amount of active ingredient in the formulation. As a general rule, active ingredients are quite stable in the concentrated formula sealed in the container. But there are storage circumstances that would predictably lead to changes in the concentrated formulation that cause products to become unstable.

For example, the product could thicken because the solvent evaporated, which could make the product difficult to pour, or cause the particles to clump and clog nozzles. In turn, these issues could cause poor mixing, foaming issues, and poor dispersion and suspension of oils and solid particles in the spray dilution.
In summary, pesticide manufacturers invest years of research and development and millions of dollars to develop new formulations and secure the necessary government registrations. However, even more important to a product’s success is its ability to easily and reliably control pests. Manufacturers have a vested interest to serve their customers by providing products that meet the highest standards for quality, user safety, and consistency of performance. Products that are unstable or do not perform up to expectations will not attract repeat buyers over the long term.
Stability Linked to Formulation Components
Pesticide formulations must allow for safe handling, dose control, storage, and field performance. Formulating a product involves adding various inert ingredients (non-active materials), combined with some mechanical processing, to prepare an easy-to-use product. For this reason, product stability depends not only on the active ingredient, but on the stability of the inert ingredients included in the formulation recipe.
Diluted formulation types before and after agitation
A formulation is a mixture that contains active ingredients and inert components that are effective and shelf-stable.
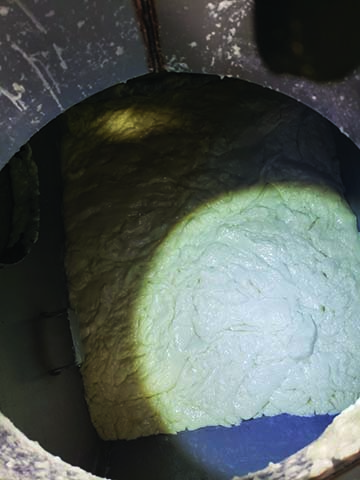
Manufacturers must decide which formulation type they prefer for the active ingredient, then select appropriate government-allowed inert ingredients to prepare their formulations. The first requirement is to prepare a concentrated mixture that contains the active ingredient. If the active ingredient or any of the inert ingredient become unstable, then the product can fail to perform.
When people use products beyond their shelf life, the products may suffer dispensing problems, poor dilution, loss of potency, or spray application difficulties. Each formulation type is unique in composition, and its responses to different storage conditions can vary widely. For example, liquid solutions — like soluble liquid (SL) or emulsifiable concentrate (EC) — tend to be shelf-stable longer than a multiphase formulation — like suspension concentrate (SC) or concentrate emulsion in water (EW). A multiphase formulation is simply solid active ingredient particles that are suspended in water or oil-phase active ingredient particles pre-emulsified in water. But under harsh storage conditions, normally stable products can be rendered unsuitable for continued use.
Manufacturers examine formulations for changes in their chemical components (such as their effects on active ingredients) and for changes in the physical properties of the inert ingredients (such as clumping, failure to disperse, settling, pourability). The examples that follow summarize some of the stress-tests manufacturers conduct on pesticide formulations to determine whether the active ingredients, inert ingredients, and formulation mixtures remain stable over a wide range of environmental conditions.
Testing the Effects of Heat
As they develop new pesticide products, manufacturers continually evaluate them using accelerated aging test methods. Although this may sound complicated, these tests simply assess a formulation’s stability when stored at high temperatures. Because manufacturers can complete these studies in much less than two or three years, they are called accelerated aging tests. Such tests are typically most useful for predicting an active ingredient’s stability.
Manufacturers conduct accelerated aging tests by subjecting their products to temperatures of 122°F (54°C) for at least two weeks and/or temperatures of 104°F (40°C) for eight weeks. The 122°F accelerated testing for two weeks normally predicts about two years of ambient storage stability. In addition to predicting shelf stability, the results help manufacturers understand how sensitive the formulation is to much higher than normal expected use temperatures when they are stored.
It’s important to remember that these tests generally approximate two-year shelf-life under normal product use — they are more a rule-of-thumb indicator. In addition to accelerated aging tests, the EPA also requires real-time product stability testing before they finalize a product’s registration. Real-time testing ensures that a product’s formulation and packaging are compatible at ambient storage conditions of 68°F (20°C).
Testing the Effects of Cold
Freeze/thaw testing is perhaps the highest physical stress test for liquid pesticide products. It is common for users to store pesticides in unheated, outdoor storage facilities where they can freeze. Cold temperature tests are meant to mimic those storage conditions. In contrast, storing pesticide formulations in temperature-controlled facilities that protect them from freezing can significantly extend their useful shelf life.
Manufacturers conduct cold storage tests (less than 20ºF or -6.5°C) and repetitive freeze/thaw cycle tests (from 20ºF to 100ºF or from -6.5°C to 40°C) for eight weeks to force the formulations to solidify. After thawing, the products are expected to recover their original forms.
These tests are especially challenging for water-based formulations such as suspension concentrates (SC) and suspoemulsions (SE), because solid water crystals form, and then melt upon warming. Cold storage testing for soluble liquids (SL) and emulsifiable concentrate (EC) products can cause the dissolved active ingredients to crystallize and precipitate out of solution. It is important to redissolve the crystals upon warming prior to using the product. Undissolved crystals (even after agitation) can create problems with dose measurement for soluble liquids. In EC products, crystals can cause problems with spray mixing and plug nozzles. In order to avoid crystallization problems, many EC formulation labels include cold temperature storage restrictions.
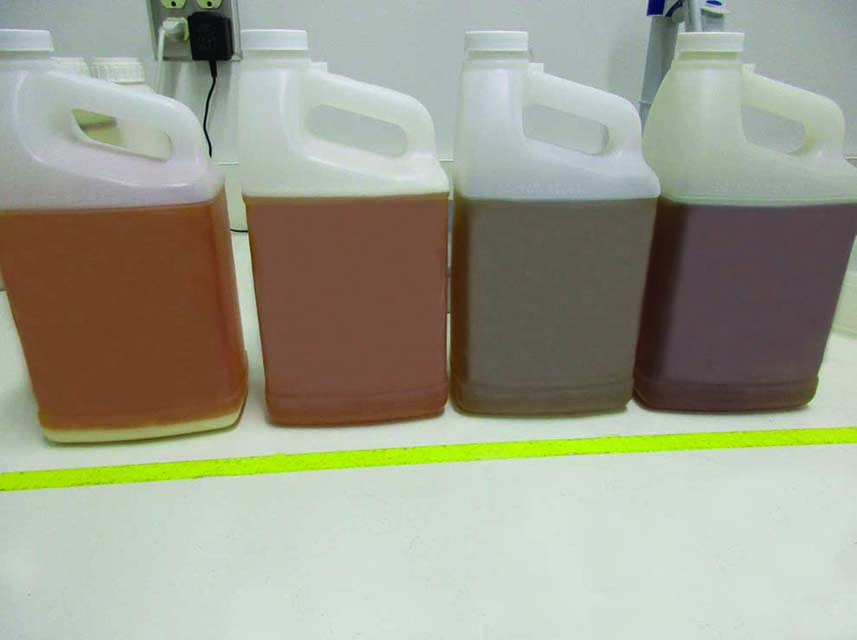
Testing Viscosity at Cold Temperatures
The viscosity of liquid pesticide formulations is another important property. For product development, the ideal viscosity offers easy handling and mixing, but provides enough robustness to prevent the formulation from separating. Manufacturers prefer that a liquid product’s viscosity remains consistent during storage testing.
Selecting the proper inert ingredients and how much active ingredient to combine in these formulation is critical. Notable changes in a formulation’s viscosity are early predictors of longer-term product separation or undesired thickening issues. The viscosity of most formulations will normally change when kept at different storage temperatures. Generally, formulations kept at high temperatures have reduced viscosities (flow easier), while those kept at low temperatures tend to become more viscous (thicker).
Cold temperature storage and handling properties are critical for some products, especially bulk product formulations that require rapid pumping to efficiently transfer the product from a tanker truck to a bulk storage tank. Packaged products that become highly viscous are slow to pour, dilute, and mix — they also may hinder proper package rinsing.
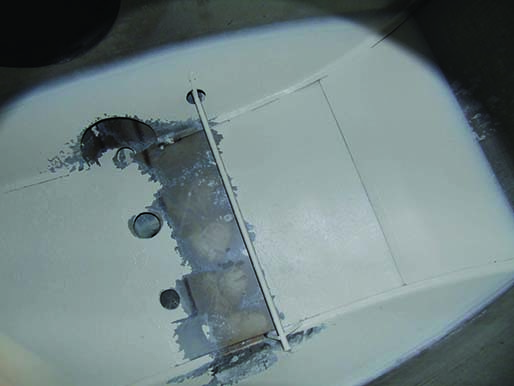
If a viscous product tends to quickly settle to the bottom of the spray tank, that can cause more serious concerns. Settled products may require extended and more vigorous agitation to ensure uniform spray application mixtures. Settled products also may result in nonuniform product applications and make it more challenging to clean out storage and application tanks.
Testing Particle Size Stability
Formulations that contain suspended solids must meet specific particle size specifications. Those particle sizes are important, so that suitably sized particles are capable of flowing through spray application equipment via a nozzle. Optimal particle sizes also ensure the most effective coverage of target pests. Product storage tests also validate the particle size — their goal is to determine that particle size does not change with extended storage times or normal variations in temperatures.
Products that fail to dissolve or suspend can plug filters and nozzles. This can affect spray coverage and ultimately create maintenance issues that lead to significant down time.
Testing Particle Suspension in Spray Mixtures
For formulations that contain solid particles, another standard performance test is determining percent suspensibility. This test measures the physical stability of a spray dilution when it is left unmixed for 30 minutes, simulating poor tank agitation. Generally, it is desirable to keep at least 70 percent of the total particle mass suspended over this test period. Suspensibility is a critically important test both for liquid products that contain suspended particles and for water dispersible granule formulations and wettable powders.
As products age, or are subjected to varying storage conditions, their suspensibility performance can change. If the product’s particle size changes during storage, it can result in diminished activity, poor control, and poor dilution stability. More severe changes in particle size can lead to buildup on filters and clogged nozzles. Suspensibility tests are also often repeated in water that contains varying levels of minerals that might be found in different water sources. Manufacturers often select the inert surfactant ingredients based on results from these evaluations.
Manufacturers also commonly run a second, related test, referred to as resuspensibility. This test lets the diluted particle suspension sit undisturbed overnight, and then measures how much mixing is required to redisperse the particles that have settled out in the tank. As you might expect, manufacturers (and users) want such sediments to remix quickly once they start agitating the spray mix.
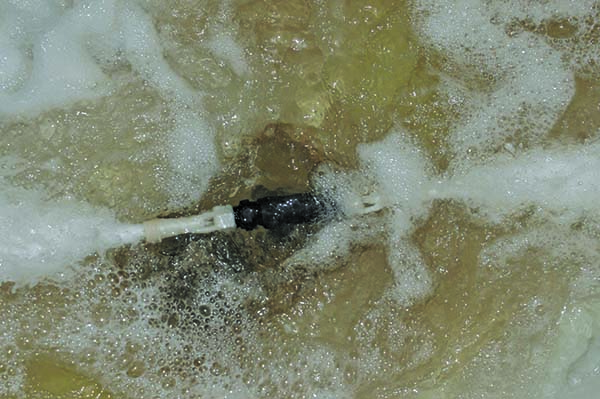
Testing Packaging Materials
EPA formulation registration requirements require manufacturers to test the formulation in their designated commercial package. Testing whether the packaging material is compatible with the product formulation also is in-depth. This assures that the package adequately protects the product and that the package does not break down or react with the formulation.
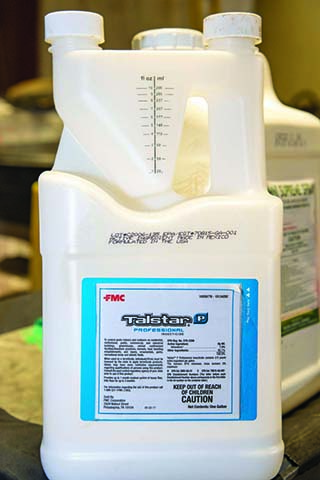
Manufacturers run these compatibility tests at multiple temperatures and timepoints. They test materials and plastics for the bottles, caps, and seals. They test many materials, but not all of them suitably protect the product or are compatible with the pesticide product formulation. To test different packaging materials, a manufacturer will fill the proposed container with the formulated product, then inspect for any splits, cracks, and softened areas over time on the package’s components.
Manufacturers test all parts of their product’s packaging to make sure the materials are compatible with the formulation. (Top) Testing the cap foil. (Middle) The yellow on the bag is a discoloration of the plastic because of product permeation. (Bottom) A plastic container that has failed.
Dry formulations are often sensitive to moisture and may absorb water from humid air. For this reason, water dispersible granules require moisture-proof, barrier-sealed packaging. When dry formulations are exposed to humid air, they absorb moisture and become unstable. Absorbing moisture may result in granules that form lumps that will no longer disperse completely when added to the spray tank. Consequently, this causes mixing and spray applicating problems for users.
It is important to keep dry products in water-tight packages to preserve their shelf lives. In the case of dry fertilizer formulations that are coated with a pesticide, exposure to moisture can solidify the granules into a brick, rendering the product unusable.
Don’t Cut Water-soluble Packaging
You should never store partially used, open bags of water-soluble products. Keep pouches in their sealed bags until you plan to use them to prevent them from getting wet.
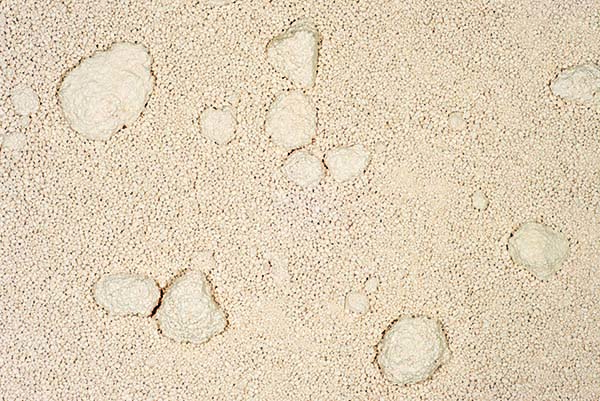
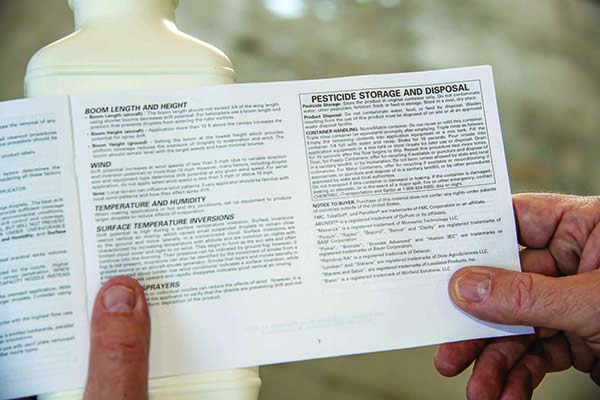
Storage Restrictions on Labels
In some cases, manufacturers are not able to build in all the desired product attributes into a formulation. In such cases, product storage restrictions may offer acceptable solutions.
Here are some storage restrictions taken from actual labels:
• Do not store above 100°F for extended periods of time. Storage below 20°F may result in formation of crystals. If product crystallizes, store at 50°F to 70°F and agitate to redissolve crystals.
• Store above 5°C [41°F]. Keep unused water-soluble bags in resealed original container. Keep packages dry at all times. Keep packages out of rain. Keep from freezing.
• Keep from overheating and freezing. Store between 40°F and 77°F. Product should be used promptly after opening the package. Apply any unused product within 4 months of opening.
• Do not store for more than 30 consecutive days at an average daily temperature exceeding 100°F. If allowed to freeze, shake well to ensure the product is homogenous before use.
• Store above 10°F (-12°C) to keep product from crystallizing. Crystals will settle to the bottom. If allowed to crystallize, place in a warm room 68°F (20°C) for several days to redissolve and roll or shake container or recirculate in minibulk containers to mix well before using.
These examples demonstrate that products have very specific storage restrictions and instructions.
ANSWERING THE QUESTION: ‘IS THE PRODUCT STILL GOOD?’
What are the differences between the expiration date and shelf life?
Generally, U.S. pesticide manufacturers do not print expiration dates on their containers. There are exceptions, such as disinfectants (including, germicides). Furthermore, limited warranties do not prescribe expiration dates.
Pesticide product manufacturers generally design their formulations to remain both chemically and physically stable for at least two to three years in their original and sealed packages. This ensures sufficient time for products to move through nationwide distribution channels to end users. This also provides farmers and commercial pesticide application industries some added time to use the products after they are sold without any concern about product integrity and effectiveness.
Most pesticide products do not list specific expiration dates. There are exceptions, like disinfectants, which are mandated by the EPA to carry expiration dates.
Storing Products Within the First Three Years
A manufacturer’s goal is to ensure that customers who use their products during the first two to three years see no changes in the physical condition, handling, or performance of the products’ formulation or packaging. In general, the two- to three-year period becomes the unofficial expiration and warranty date for most pesticides.
You can assume that if you don’t see storage restrictions on the label that the formulation is rather stable. But just to be on the safe side, you should not keep products in inventory for more than three sales seasons.
Consider the following storage recommendations to ensure that products remain effective for use:
• Read storage directions before purchasing pesticide products to make sure you can comply with them
• Follow pesticide label storage restrictions to ensure product stability
- Store pesticides in controlled environments to prevent temperature extremes
• Use all products within the season of purchase
• Don’t buy more than a two-year supply
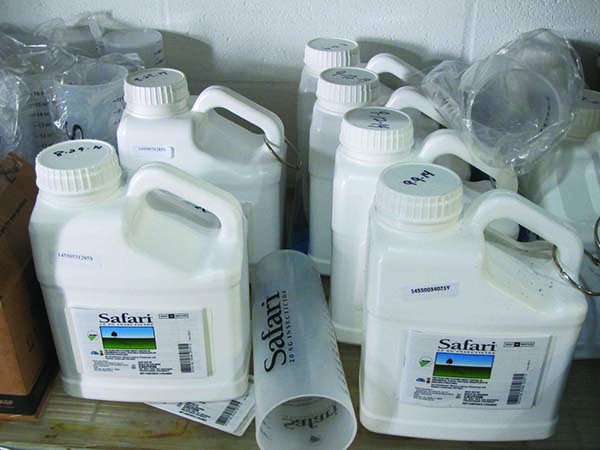
• Place the year of purchase on containers as a visual cue to identify the age of stored products
• Rotate the stock on the shelf, oldest to front
- When switching to new formulations, first use up the product you are replacing
- Keep products sealed and lids tight to prevent evaporation and contact with moisture
- Shake all containers before using them to ensure active ingredients and coformulants (inerts) are uniformly mixed
- Use opened containers and bags the same season
Some products require users to shake the containers to mix up the formulation. We suggest shaking all products in this manner before use just to ensure a well-mixed product.
Many storage facilities accumulate opened containers that remain unused for years. The longer opened containers and bags remain in storage, the greater the odds they will not work as expected.
Evaluating Products of Questionable Age
There are many reasons why products remain in storage longer than three years, including:
• Managing product inventory is not a priority
• The user bought too much product
• The user switched to a replacement product without using up current inventory
• The product has limited use as part of a tank mix
• The user is dissatisfied with a product’s performance
• Product labels partially torn or missing
• The EPA cancelled the product registration, and the time to use up the existing stock has passed
• The product was misplaced and found after a cleanup
Many formulations are designed to be stable and effective for as long as the chemistry allows, but none are permanently stable. Still, we ask the question: Is this product on my shelf still good? If the product is still sealed in its original container and it’s within two or three years of purchase, it seems like the answer is an easy “Yes.” Just the opposite is true for opened products beyond three years.
The question then should be: When does a product go from being effective to being a candidate for disposal? While the two- to three-year storage period may have long expired, that doesn’t necessarily mean the product is no longer effective. The answer is nearly impossible to pinpoint, because there are so many interactive variables, including the product’s age, whether the container was opened, and the conditions under which the pesticide was stored.
It can be quite challenging to determine if the product will deliver consistent results, which ultimately is the question you want answered.
Let’s say you have 10 unopened, 2.5-gallon pesticide containers that have been stored for an unknown number of years. You remember buying the product, but you switched to a different and more effective product soon afterward. You simply want to know whether the product in those containers is still effective, so you can at least recoup your investment in the product and avoid disposal costs.
When deciding, consider the following:
• Find out if the product is still registered (is it still legal to use?)
• Check the product’s physical characteristics
• Conduct a jar test
• Contact the manufacturer or distributor representative
• Test the product under field conditions
Find Out if the Product Is Still Registered
If a product is no longer state or federally registered, then all of the other factors to consider are moot. It does not matter if the product is viable or not — if it is no longer registered, you cannot use it.
You can check a product registration list with the Office of Indiana State Chemist (OISC) or your state’s department of agriculture to determine if the company has paid its annual fee. If the product remains registered, then the you may use the product. If you have lost the product’s label or the label is unreadable and you can’t determine its identity, then it is a candidate for disposal.
Check the Pesticide’s Physical Characteristics
See if you can determine whether the product looks like it did when you first used it. Assess for the color, unusual odors, thickening, top-clearing, or noticeable sediment formation. If the ingredients have separated out, try gently inverting the closed container 5-10 times. If the product remixes and appears uniform, the product may still be acceptable to use.
However, you should consider disposing of the product if you observe:
• Clumping
• Bottom accumulation
• The product does not resuspend
The product has an unusual odor or color
• Separated layers remain after mixing
• The package has been previously opened
• A hard-pack sediment has formed on the bottom
Conduct a Jar Test
A jar test allows you to determine if a product’s ingredients mix well and remain uniform. To conduct a jar test, begin by mixing a minimum amount of product (follow label directions in a small, clear container). Let the material sit for at least 30 minutes, and observe what happens.
Does the product settle out of solution within 5 to 10 minutes? Repeat the test to see if the solids in the bottom resuspend or redissolve. If the product fails to suspend, it is a candidate for disposal.
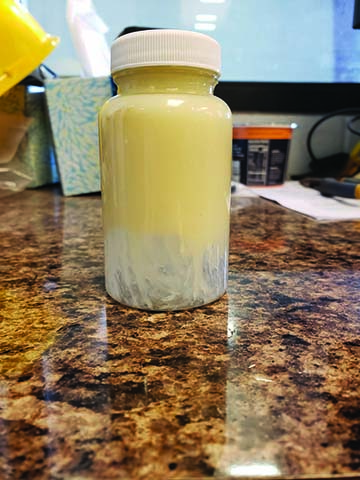
For more details about conducting jar tests, see Avoid Tank Mixing Errors: A Guide to Applying the Principles of Compatibility and Mixing Sequence (Purdue Extension publication PPP-122), available from the Education Store (edustore.purdue.edu) or Purdue Pesticide Programs (ppp.pudue.edu)
Contact the Manufacturer or Distributor Representative
If you have questions about the viability of a product, contact the manufacturer’s customer service information found on the label. When you ask about the product’s storage stability, you may be connected to a specialist who can better address your question.
Before you seek advice from the manufacturer or distributor, you should be prepared to answer a few questions from them. Specifically, they will want to know the name of the product, its EPA registration and establishment numbers, and the bar code stenciled directly on the container.
The manufacturer can use the bar code to determine the year and month the product was made, where it was packaged, and the batch and lot numbers. Often, a dribble down the pesticide container will smudge a portion of this code. If that code becomes indiscernible, then the product should be considered a candidate for disposal.
Once you provide all the relevant information to the manufacturer, they may be able to determine if the product is within its window of usability. The longer a product has been in the marketplace, the more likely the manufacturer has historical shelf-life information to help guide them in answering your questions about stability. The manufacturer may also ask you about your jar test results. If you observed that the product did not mix well, the manufacturer may instruct you to properly dispose of the product.

You Need A Decoder Ring to Determine a Product’s Age
Finding the expiration date on a product container is impossible for end users. That’s because manufacturer codes include dates that only they can decipher. By examining the lot number stenciled on the container, the manufacturer can track where it was made, the date it was placed in the container, and the batch. A few companies will list the manufactured date on the container.
While that will not list the expiration date, it will give you the product’s age. This is an important first step in knowing if the product is still viable.
Test the Product Under Field Conditions
The only failsafe way to determine whether the product is still effective is to apply it in the field. Applying the pesticide on a small portion of a site will allow you to determine if the product still works without causing any unforeseen effects such as phytotoxicity. If the product does not provide control, or causes negative side effects, then it is a candidate for disposal.
However, do not conduct such field tests with fungicides. If the fungicide is no longer effective, the plants you wanted to protect may already be infected with the disease. In many cases, there are no rescue treatments to treat a disease once it has infected the plant. If there is any doubt with a fungicide, it may be a candidate for disposal.
WHEN DISPOSAL IS THE ONLY ALTERNATIVE
If your product has failed the question, “Is this pesticide on my shelf still good?“ then your only viable alternative is to properly dispose of it.
Choosing to apply an “old” product may open you to liability concerns caused by uncontrolled weeds, continued damage from termites, or even destruction of natural habitat if the product does not control invasive species.
An EPA-cancelled active ingredient will normally have a “drop-dead” end-sale date that allows the product to be used according to the label. After that date has passed, the product can only be disposed by a company that has obtained the necessary hazardous waste permits
The Office of Indiana State Chemist holds summer pesticide disposal days around the state, during which people can bring cancelled and unwanted pesticide products to the site. These products will be properly disposed of by a licensed contractor at no cost, or at a nominal fee for large quantities.
For more information, directly contact the OISC — oisc.purdue.edu.
Many other states have their own disposal programs. In Canada, Cleanfarms is a nonprofit that removes unwanted or obsolete pesticides — cleanfarms.ca.
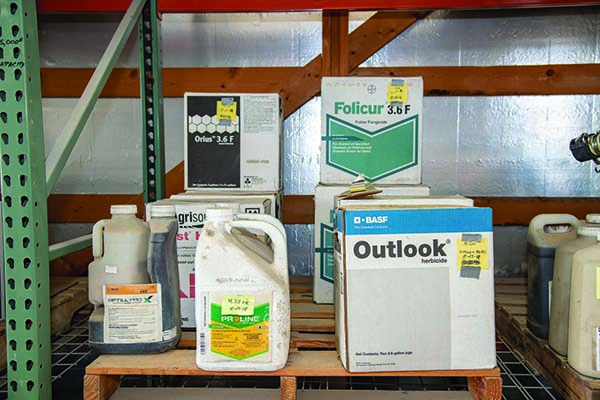
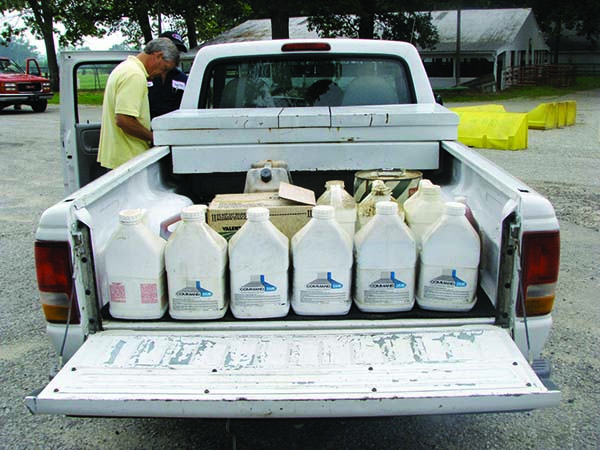
It Is Your Discretion to Use or Dispose of Product
The caveat to answering whether a product is still effective is that no one can guarantee how well a product will work that’s been left in storage for any length of time. The most you can expect is that answering the question is a “best guess” judgement based on the information available to them. The responsibility of whether to use the product is left to the user’s discretion.
It is important to note that manufacturers will seldom take and analyze samples involving a few containers. Instead, they will spend their resources when there are pallets of stored materials or hundreds of gallons of product involved.
Consider the value of replacing the product with the cost if the product does not perform or if it creates application problems.
Warning! Warning! Warning!
Be sure to monitor the condition of the packaging materials with products that are slated for disposal. We highly recommend using secondary containers as a way to contain spills that might happen if the product’s metal, plastic, or paper containers release their contents.
Conclusion
As an end user, you can control some of your chemical costs by purchasing and using what you need for a given season and then storing the product according to label directions. This is easier said than done, because pesticide formulations often change, causing the product to be “shelved” in preference for what’s new.
Over time, pesticide storage facilities often become a mish-mash of older, forgotten, and some partially used products that do not come with expiration dates stenciled on the containers. Managing this “old” inventory may lead you to ask some time-consuming and expensive questions. Is this product still legal to use? Does this product still control pests? Does this old product cause off-target injury? How much will it cost to legally dispose of the product?
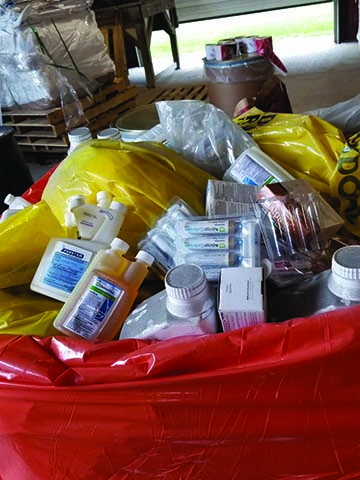
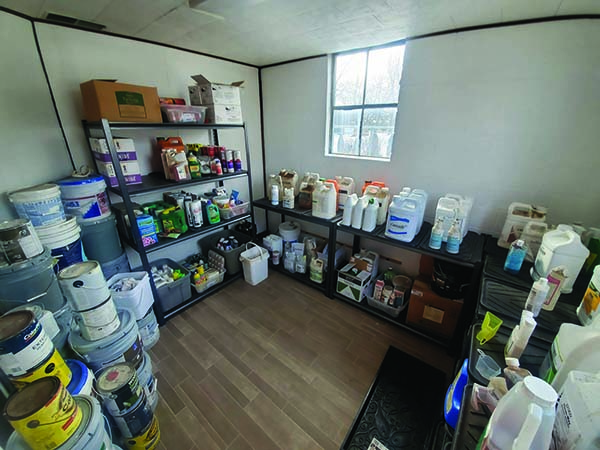
This publication provided common-sense guidelines that can help you better manage your pesticide product inventory. Whether it is putting a purchase date on the containers or rotating stock, these simple-to-implement procedures can help keep your inventory “fresh.” Keeping your formulations in tip-top condition are just as important as calibrating your equipment, training your employees, and serving your customers. By better managing your product inventory, you will no longer have to ask, “Is this pesticide on my shelf still good?”
Following the inventory management guidelines in this publication can reduce the number of questionable products in storage.
This not only saves money, but ensures that the products you apply are effective, which keeps your customers happy
Find Out More
Purdue Pesticide Programs offer a number of publications on related topics to help you manage your operations better. All publications are available from The Purdue Extension Education Store: edustore.purdue.edu 765-494-6749
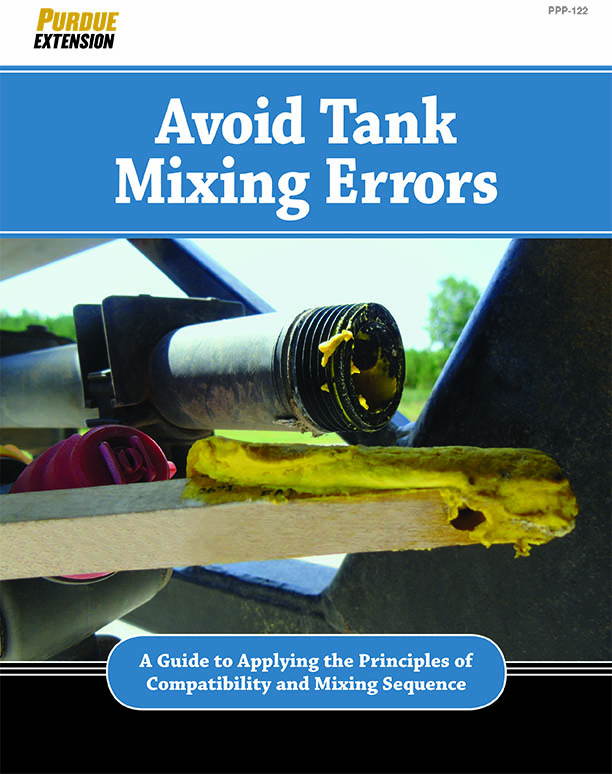
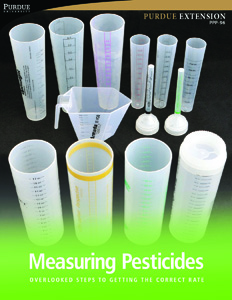
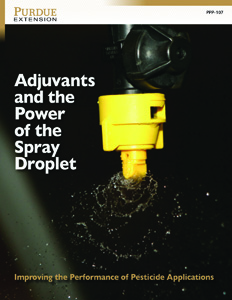
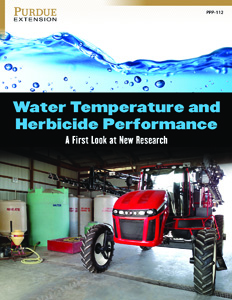
Acknowledgments
Thanks to Dawn Minns for graphic design and Adduci Studios for illustrations. Thanks also to the following individuals who provided valuable comments and suggestions that improved this publication.
Beth Carter, Office of Indiana State Chemist
Mike Corbitt, Veseris
Jason Deveau, Ontario Ministry of Agriculture, Food and Rural Affairs
Clarence Hermansky, CPC Formulations, LLC
Aaron Kreider, Office of Indiana State Chemist
Glenn Nice, University of Wisconsin
John Phillips, Phillips Farm Sales and Service
Ed Spanopoulous, Lake and Pond Biologists
Daniel Wright, Bayer CropScience
DISCLAIMER
This publication is intended for educational purposes only. The authors’ views have not been approved by any government agency, business, or individual and cannot be construed as representing a perspective other than that of the authors. The publication is distributed with the understanding that the authors are not rendering legal or other professional advice to the reader, and that the information contained herein should not be regarded or relied upon as a substitute for professional consultation. The use of information contained herein constitutes an agreement to hold the authors, companies or reviewers harmless for liability, damage, or expense incurred as a result of reference to or reliance upon the information provided. Mention of a proprietary product or service does not constitute an endorsement by the authors or their employers. Descriptions of specific situations are included only as hypothetical case studies to assist readers of this publication, and are not intended to represent any actual person, business entity, or situation. Reference in this publication to any specific commercial product, process, or service, or the use of any trade, firm, or corporation name is for general informational purposes only and does not constitute an endorsement, recommendation, or certification of any kind by Purdue University. Individuals using such products assume responsibility that the product is used in a way intended by the manufacturer and misuse is neither endorsed nor condoned by the authors nor the manufacturer.
